| Encoders and proximity sensors:
Encoders and proximity sensors
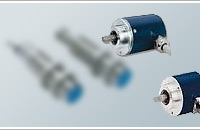
Proximity sensors are elements that are applied in the industrial automation systems for rectification of the objects. Depending on the object, that must be rectificated, appropriate type of proximity sensor, reacting for specific peoperties (a kind of material, colour an so on) is chosen.
Sensors can be connected with counters, tachometers inputs of controllers and so on . |
Inductive sensors
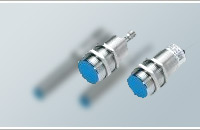
Inductive proximity sensors are elements of automation, that react if you introduce metal in the zone of their work.
They are commonly applied in the industrial automation systems for precise chracterizing location of movable elements of machines and appliances. They are characterized by large work security and reliability in the hard conditions of the surroundings (too much dust, humidity and so on).
|
Spark-proof proximity sensors
Spark-proof proximity sensors are applied in the places where the danger of ignition, fire or explosion is quite large. An utput signal of PCIN sensor is change of the current, which is recognized by the intensifier. |
Capacitive sensors
Capacitive proximity sensors are applied for example to control the level of the liquid in the container (through the wall of plastic, too), to detect granular and powder material, to detect plastic, glass, wooden and metal elements. |
Optical sensors
Optoelectronic sensors are elements of automation, that base on the rule of sending the sunbeams by the transmitter and reciving it by the receiver.
These sensors react for the objects, that cut the sunbeam between the transmitter and reciver or for the sunbeam that reflects from the object. They are applied for location control of movable elements of machines and for identification of the objects that are placed in the zone of sensors work, for exmple transport movable tapes, to define the level of liquids and lose materials. Thy are characterized by wide zones of detecting sensors. |
Reflective optical sensors
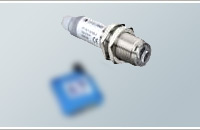
The advantage of these sensors is placing in one casing both reciver and transmitter without a need to use a reflector. That assures easy montage, regulation and wide power of these sensors.
|
Reflective sensor eliminating the influence of the background
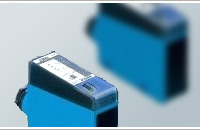
Reflective sensor that eliminate the influence of the background detect on the same way bright and dark objects and the zone of their work is precisely regulated (even with th eaccuracy to 0,1 mm).
These sensor are irreplaceble by detecting elements that move near to the background or substrate, that shoudn't be detected by the sensor. They're reliable by detection of elements that are made of glass or transparen materials. |
Optical sensors barrier
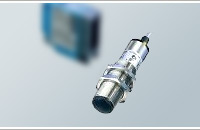 Optical sensors of the barrier type consist of two separately feeded elements: transmitter and reciver. They're situated on the one axis, that is definited by the beam of the sensor. The sensors detect objects, that appears between the transmitter and the reciver. They have the longest zones of operation in comprehension to reflective sensors (to 50m). |
Optical sensors of colour and contrast
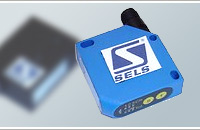
Sensors of contrast detect a contrast colour of the object and the background. Sensors of colour detect any colour of the object.
|
Optical analogue sensors
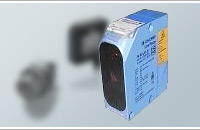
At the output of the analogue sensors we receive an analogue current or tension signal, that is proportional to the distance between the sensor and the object.
They fit to the systems that precisely measure linear size, parameters of movable and vibrating elements.
|
Optical senors cooperating with fiberglass 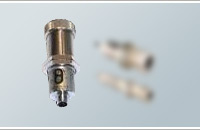
Optical sensors that cooperate with fiberglass are applied to detect objects in the places where sensors with standard casings can't be applied, and in the aggresive surrounding where the temperature reaches 250C (when the reinforced fiberglass or fiberglass in the casing of silicon is applied). Construction of these sensors causes that the mechanical connection with cooperating fiberglass (that are replacable elements) is possible. |
Ultrasound sensors
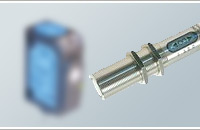
Ultrasound sensors are applied for detection of the objects and detection of transparent and non-transparent liquids first of all in the surroundings, where, because of pollution, applying optical sensors is impossible. The rule of measurement by these sensors bases on the measurment of time, that goes by between ultrasound signal and recived echo, that reflected from the barrier. The time is proportinal to the distance from the detected object.
|
Linear cameras
A linear camera passes the information on in the character of output analogue signal that is proportional to the selected parameter of the object.
It can be size of the object, a distance between moving elements, a shift of a detale from the definited referencial line, a size of a sag, deflection of the material and many other. The measurement of these parameters may be done when the object moves. The object is introduced between a camera and a fluorescent lamp and causes that the camera sees no fluorescent lamp. |
Sensor of the image
Sensors of the image are applied to detect different kinds of patterns and markers.
They have, depending on th etype, two kinds of matrix. Type FA 30 WCM PA... bases on the CMOS chip, and the series FA 30 WCC PA... bases on yhe CCD chip. The sensor have three modes of work: detection of the difference between white and black pixels in the zone of saved resolution (Contrast), detection of the difference in the grey scale (Greylevel), detection of the false pattern or deflection of the programmed position (Patern Maching/Position Control). Their digital inputs let introduce the signal (from other sensor) realising control moment (of the pattern) with the possibilty of using the built-in source of light. The sensor has a software for PC, thanks to that you can see the object, programme and read-in settings to the memory of the sensor.
|
Inteligent adapters
Inteligent adapters are such appliances, that are assembled between any sensor with analogue output with 10-30 VDC feeding and conector. They extend functional skills of the sensor.
Cooperating with the sensor, inteligent adaptors let count the elements, make time of sensors work longer, ignore short disturbing impulses, control rotating and linear speed, change polarization and output functions of the sensor, increase load-capacity of the sensor. Inteligent adaptors can be connected in series, than functions of them becomes more multifaceted.
Encoders
Encoders let convert an angular position. . On account of the signal that is created at the output of them we can distinguish:e
- rotating-impulse converters (incremental encoders)
- rotating-code converters (absolute encoders)
Rotating-impulse converters are rotating appliances. At the input the generate double series of impulses, that are shifted to each other about 90. It let check the direction of the roller turns. By each turn of the axis of the encoder specified number of impulses appears at the output.
If you have an encoder with the impulsation 1000 imp/turn, there will be an impulse at the output by the turn of the roller axis every 360/1000=0,36.Rotating-impulse converters are applied in the systems, where specified dependence between one turn and othe phisical size appears.
Connecting at the input standard impulse counters we can create easuring systems of length and rotating speed by one-siede direction of the turns. Applying counters with quadrature input we can count the length by difference of the directions.
Rotating-code converters are made as one- and multiturn appliances (limited number of impulses). At the output, depending on the position of the angular roller they generate a code signal. It let precisely estimate turn angle and number of turns (for multiturn encoders). You may say, that absolute encoders save exact angle position of the axis.
If we have a multi-turn encoder with resolution of 25 bits (13 bits fall to each turn and 12 to number of turns) we can characterize the angle position wit the accuracy to 1/8192=0,0012 for 4096 turns).
Absolute encoders are applied in the systems of positioning, callibration of machines and robotics.
| |